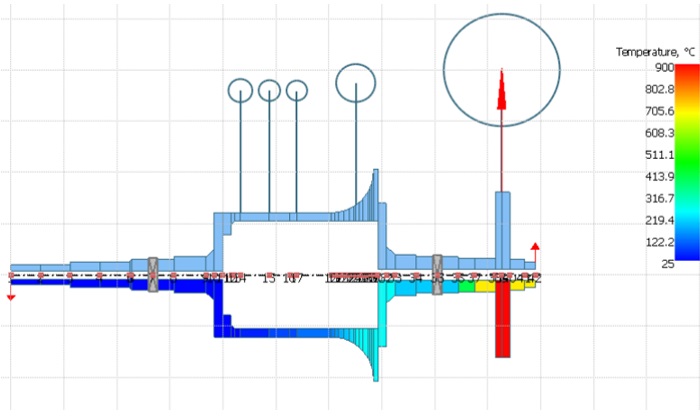
High-speed rotating machines play a key role in various industrial applications, including aerospace, power generation, and manufacturing. However, designing these machines presents several rotor dynamics challenges that must be addressed to ensure efficiency, reliability, and safety. In this article, we will explore the key challenges in rotor dynamics and common analysis principles used across industries.
Rotor dynamics analysis is crucial for ensuring the reliability of high-speed machines. Rapid lateral rotor dynamics analysis is particularly important during the preliminary design stage, while in-depth verification is necessary at the final stage or when confirming the reliability of an existing design. A solid understanding of rotor dynamics helps engineers develop accurate rotor and bearing models, predict potential issues, and implement effective solutions early in the design process. Various analysis approaches, including beam, 2D, and 3D methods, offer different levels of insight into rotor behavior, with comprehensive analysis at later stages ensuring long-term reliability.
Industry-Specific Challenges and Common Solutions
Each industry has specific requirements for high-speed rotating equipment, driven by operational conditions, safety regulations, and efficiency goals. However, despite these differences, rotor dynamics analysis serves similar purposes across all fields, such as predicting and mitigating resonance issues, ensuring rotor stability, optimizing bearing performance, and managing thermal effects. Regardless of the application, effective rotor dynamics analysis enhances reliability, prolongs equipment lifespan, and minimizes maintenance costs.

Figure 1- Example of aero engine [1]
Industry Standards and Rotor Dynamics
Industry standards, such as those outlined by the American Petroleum Institute (API), provide essential guidelines for conducting rotor dynamics analysis. These standards define critical parameters, including allowable vibration levels, bearing design criteria, and stability requirements. By adhering to API guidelines [2], engineers can ensure that rotating machinery meets industry-specific performance and reliability expectations. The API standards highlight key aspects of rotor dynamics analysis that are necessary to obtain accurate response predictions and mitigate potential issues.
With these foundational principles in mind, we can now explore the key challenges in rotor dynamics and the methods used to overcome them.
Key Challenges in Rotor Dynamics
Resonance and Critical Speeds
Excessive vibrations occur when a rotor operates near its critical speed, where natural frequencies align with operating frequencies. This can amplify oscillations, leading to severe structural damage or failure. Engineers must accurately predict these critical speeds using computational simulations and testing methods. To mitigate resonance risks, solutions such as tuning the rotor design, implementing damping mechanisms, and adjusting operational speeds are employed.

Figure 2 – Undamped critical speed and mode shape of a gas turbine calculated in AxSTREAM RotorDynamics
Unbalance and Vibration Control
Rotor unbalance occurs due to uneven mass distribution, leading to significant vibrations that can reduce efficiency and increase wear on components. If left unaddressed, unbalance can cause bearing failures and structural fatigue. Engineers apply precise mass balancing techniques, including static and dynamic balancing, to ensure smooth operation. Additionally, active vibration control systems, such as tuned mass dampers and real-time monitoring, help mitigate unwanted oscillations.

Figure 3 – Amplitude -Frequency characteristic due to unbalance of a centrifugal compressor calculated in AxSTREAM RotorDynamics
Bearing and Support System Design
Bearings play a critical role in supporting high-speed rotors, but at elevated speeds, they experience excessive heat, wear, and lubrication challenges. Traditional rolling element bearings may not suffice, prompting the use of advanced alternatives such as magnetic bearings, fluid-film bearings, or gas-lubricated bearings. These designs reduce friction, enhance stability, and enable higher rotational speeds while minimizing maintenance requirements.
Thermal Effects and Expansion
The high rotational speeds of these machines generate significant heat due to friction and aerodynamic effects. This thermal energy causes materials to expand, potentially shifting critical speeds and altering system dynamics. In extreme cases, excessive heat can degrade materials or cause structural deformations. Engineers combat these issues through the use of heat-resistant materials, thermal coatings, optimized cooling systems, and precise thermal expansion compensation strategies.

Figure 4 – Temperature distribution in a gas turbine rotor-bearing model
Material Selection and Fatigue Resistance
Repeated cyclic stresses at high speeds can lead to material fatigue and eventual failure. Engineers must carefully select materials with high strength-to-weight ratios, such as titanium alloys, carbon fiber composites, and high-performance ceramics. These materials provide durability while minimizing weight, reducing inertial forces, and improving energy efficiency. Advanced fatigue analysis and predictive maintenance techniques further enhance system longevity.
Aerodynamic and Fluid Dynamic Forces
Rotating machines are affected by destabilizing forces such as aerodynamic cross-coupling and hydrodynamic cross-coupling, which can induce self-excited vibrations and instability. Engineers use advanced simulation techniques to predict these effects and incorporate design modifications such as optimized bearing configurations and damping solutions to enhance rotor stability.
Rotor dynamics analysis can be performed using either 2D or 3D modeling techniques. While 3D analysis offers a highly detailed representation of rotor geometry and interactions, it demands significantly more computational resources and time. In contrast, 2D analysis provides a faster and more efficient way to estimate rotor behavior with sufficient accuracy for most preliminary and verification analyses. Given its balance between computational cost and practical accuracy, 2D rotor dynamics analysis is often the preferred choice unless highly detailed simulations are necessary.
Conclusion
Designing high-speed rotating machines requires a deep understanding of rotor dynamics to mitigate challenges such as resonance, vibration, thermal expansion, and aerodynamic forces. By employing advanced simulation techniques, innovative materials, and precise engineering practices, industries can develop more efficient and reliable rotating machinery. As technology advances, solutions such as active vibration control and improved bearing systems will further enhance the performance of these critical machines.
Modern software tools play a crucial role in simulating rotor dynamics responses, enabling engineers to analyze potential issues early in the design phase. These tools facilitate rapid assessments, optimize system parameters, and validate design choices with high accuracy. By leveraging advanced simulation platforms, such as AxSTREAM RotorDynamics, engineers can reduce development time, minimize prototyping costs, and ensure the reliability of high-speed rotating machines in demanding operational environments.
References
[1] https://www.mobilityoutlook.com/features/iae-an-example-of-successful-multinational-technology-consortium/
[2] API Standard Paragraphs Rotordynamic Tutorial: Lateral Critical Speeds, Unbalance Response, Stability, Train Torsionals, and Rotor Balancing. American Petroleum Institute, API TECHNICAL REPORT 684-1 FIRST EDITION, NOVEMBER 2019.