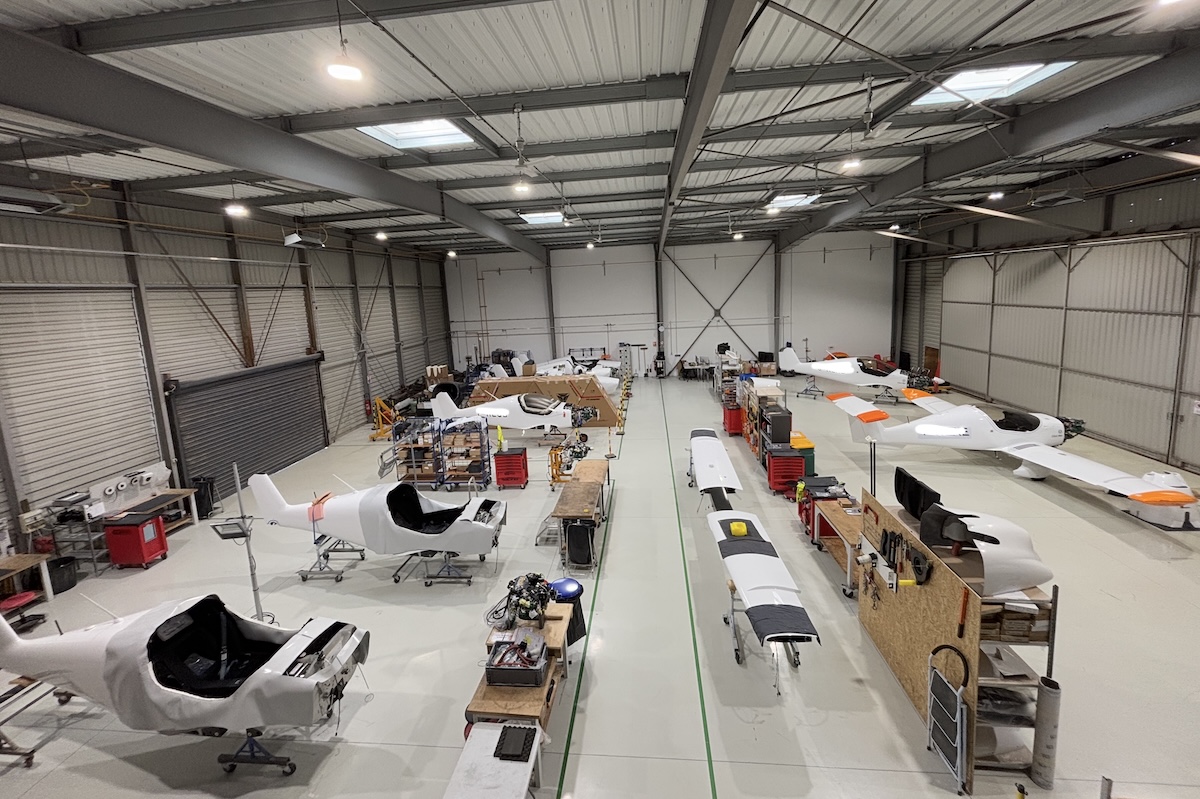
Communities along France’s Atlantic shore have long held a special relationship with the sea. What has for centuries been a region of sailors, shipbuilders and maritime traders has evolved into one of Europe’s most dynamic centers for sailing technology innovation.
The region is home to a thriving ecosystem where boat builders, equipment manufacturers, naval architects, and sailing technology startups collaborate to push the boundaries of what’s possible on water. These range from sustainable marine propulsion to revolutionary hull designs and foils to the use of advanced materials.
But what does this have to do with aviation? The world of competitive sailing provided the inspiration for Arthur Léopold-Léger and Cyril Champenois to launch one of Europe’s most promising startups in the field of general and training aviation.
Elixir Aircraft was founded in a garage in 2015, with the idea of adapting some of the technologies and methods of the advanced sailing boat industry to create a fourth-generation light aircraft that would be lighter, cheaper, safer, and more efficient to fly.
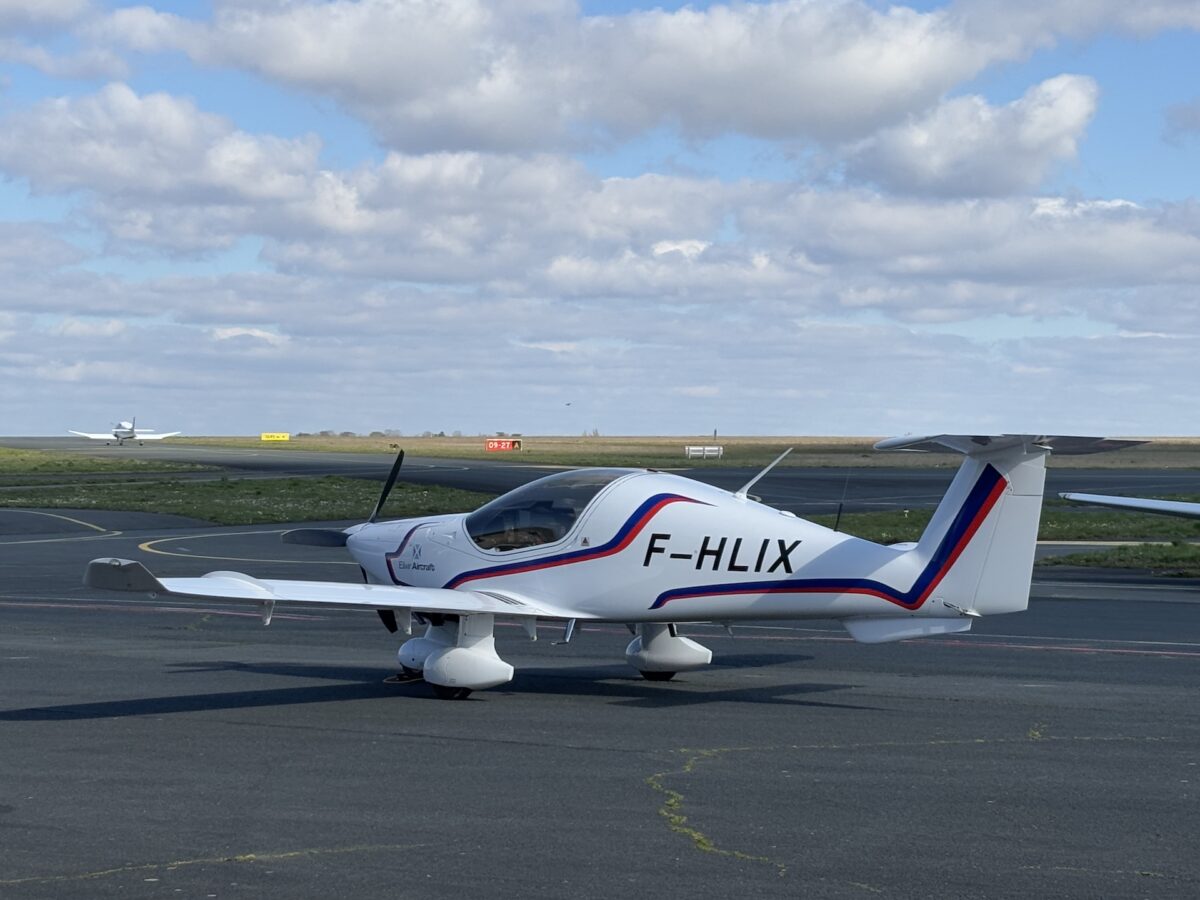
Léopold-Léger, co-founder and CEO of Elixir Aircraft, hailed from a sailing background, but also obtained an aerospace engineering degree. And it was, in fact, while working as an engineer at several aerospace companies in France that he came to the realization that the light aircraft industry was way more conservative in its approach to technology adoption than the boat builders he knew so well.
He recognized that there was an opportunity to disrupt the general aviation and flight training market with a clean-sheet aircraft and enrolled his co-founder, Champenois, in the effort. Today Champenois manages the commercial and marketing side of the business.
The macro figures indeed sound compelling. If we look at the flight training segment of the market alone, there is the unescapable fact that the aviation industry will need to train approximately 600,000 pilots over the course of the next two decades.
Furthermore, the vast majority of aircraft used for basic training in the world today are legacy models with roots that can be traced back several decades. Even if some of these types have been regularly updated with new, modernized versions, the average age of aircraft in the two to four seat category is still 47 years. In fact, most light aircraft still in service today were produced in the 1960s and 1970s. Around 130,000 aircraft were built in this category during those two decades, with production rates slowing down considerably after that. For comparison, in the 40 years between 1980 and 2020 only 70,000 aircraft in this category were built.
The market for replacements alone (according to Champenois, approximately 40 Cessna 172 aircraft are retired from service every month globally) should, in principle, keep busy the half dozen incumbents that have most of this market today (Textron, which makes the Cessna and Pipistrel brands, Piper, Diamond Aircraft, Cirrus Aviation, Tecnam and Bristell), while offering a window of opportunity to new entrants like Elixir Aircraft.
What Elixir Aircraft brings to the table is primarily its OneShot technology, which is adapted from technology used in the sailing industry. This is essentially a method to make the airframe out of one large piece of carbon, rather than assembling multiple parts as in more traditional processes. This results in a simplified, yet strong and lightweight airframe.
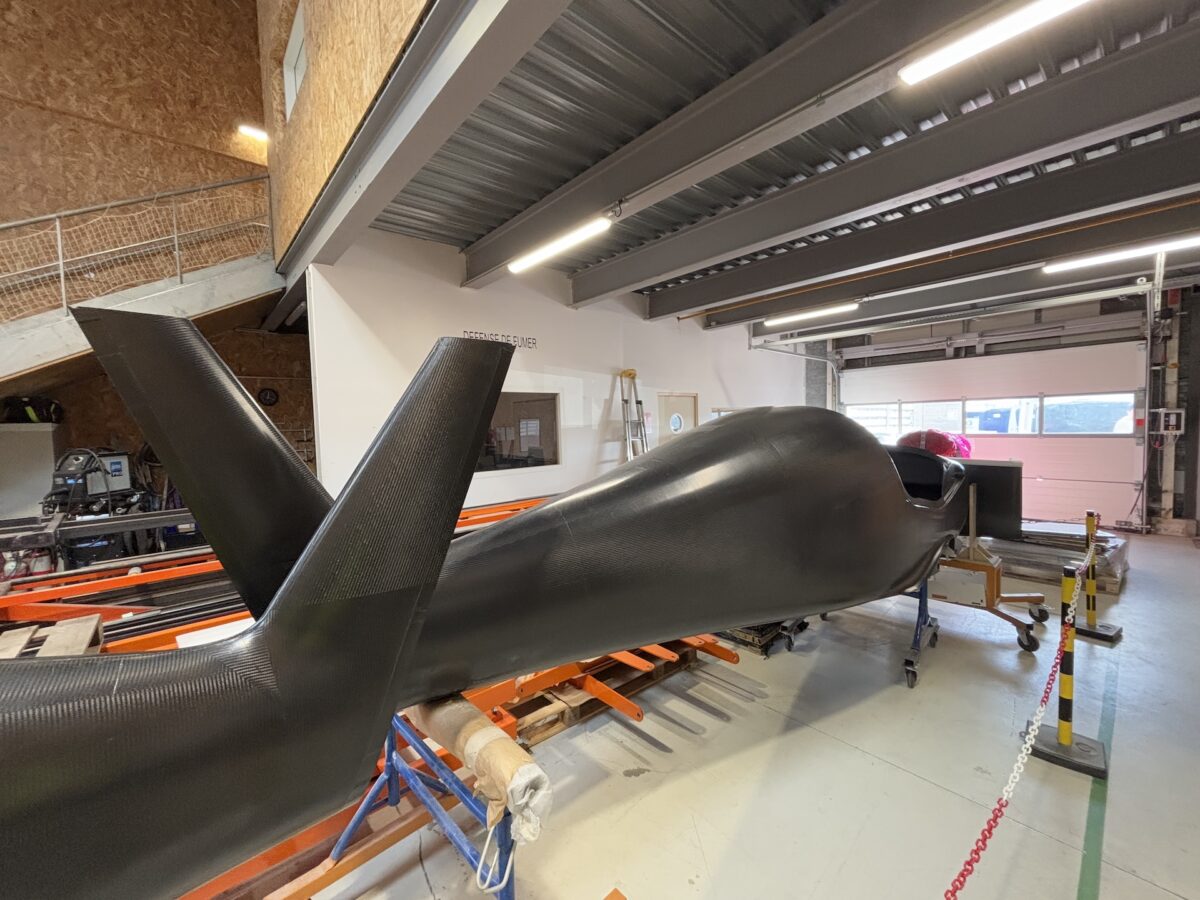
AeroTime traveled to La Rochelle, in Western France, to see in-situ how this innovative technology is being applied. During the field visit we took an exclusive look at the factory from where the first batches of Elixir aircraft are already rolling out and we were even able to experience what it is like to fly on one of them in real conditions.
From its first commercial delivery in 2022 and February 2025, Elixir Aircraft delivered a total of 28 aircraft to several customers.
Elixir Aircraft’s factory and offices are adjacent to La Rochelle-Île de Ré Airport (LRH), a small regional airport which serves this historical French city and its region.
Champenois took AeroTime on a tour of the production facilities, which, as of early 2025, are churning out two aircraft per month.
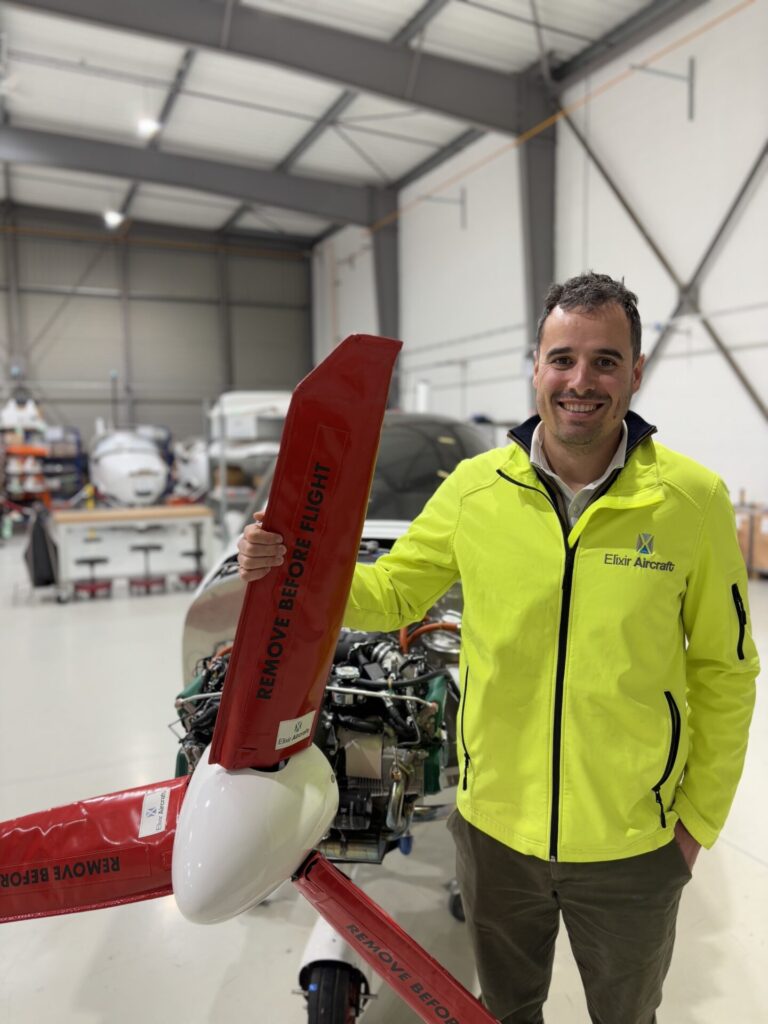
The OneShot process, a spillover from the sailing boat industry
The entire process is engineered to be relatively straightforward thanks, in great part, to the OneShot technology. During the tour, Champenois pointed out that each aircraft is made of only nine parts: the wing, the fuselage, the canopy frame, two flaps, two ailerons, a radar, and a horizontal tail.
Every element of the airframe is made with OneShot using two autoclaves of different sizes: the largest for the airframe and wings, and the smaller one to make the control surfaces.
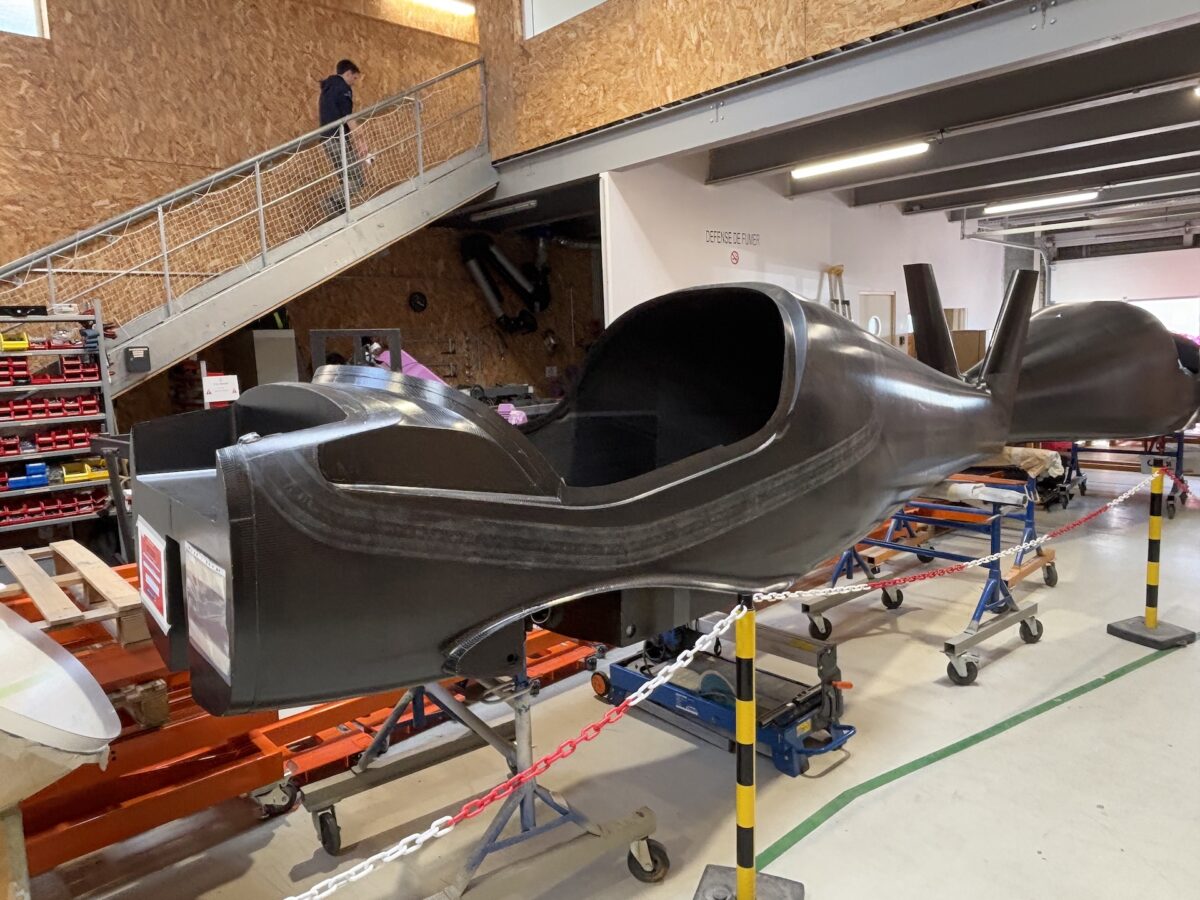
Engines are sourced from partners, with two options being offered: either powered by a Continental CD-155 diesel engine or by the Austrian-made Rotax 912iS engine. Unlike other aerospace startups, which are experimenting with electric motors and other new propulsion technologies, Elixir Aircraft has opted for conventional propulsion.
Champenois explained that, while the Elixir Aircraft could incorporate fuel cell technology in the future, the current performance of pure electric systems remains unconvincing. Instead, Elixir prefers to focus on reducing the aircraft’s emissions footprint by optimizing its design and propulsion systems.
“An aircraft that doesn’t succeed doesn’t decarbonize anything,” stated Champenois, before pointing out that Elixir Aircraft delivers a 67% fuel and emissions savings compared to legacy aircraft of the same category.
This is something he attributed to the lightweight construction and aerodynamic performance of the aircraft, as well as the advanced injection engines it uses.
Elixir’s aircraft consume an average of around 12.5 liters of fuel per hour which compares favorably with the 30 to 40 liter per hour range which is typical of most piston-engine aircraft in this category.
This economy of consumption, of course, has its financial benefits. Here, again, Elixir Aircraft has reasons to boast, with an operational cost of around €50 per hour of flight – about a quarter of that for legacy aircraft.
Safety is also paramount at Elixir Aircraft. Champenois explained how designing a clean-sheet aircraft also offered an opportunity to embed a number of state-of-the art safety features. For example, by adding avionics that prevent unintentional spinning, which is one of the major causes of accidents in legacy aircraft. It also has double slotted flaps to enhance lift and control when landing, as well as non-exploding fuel tanks.
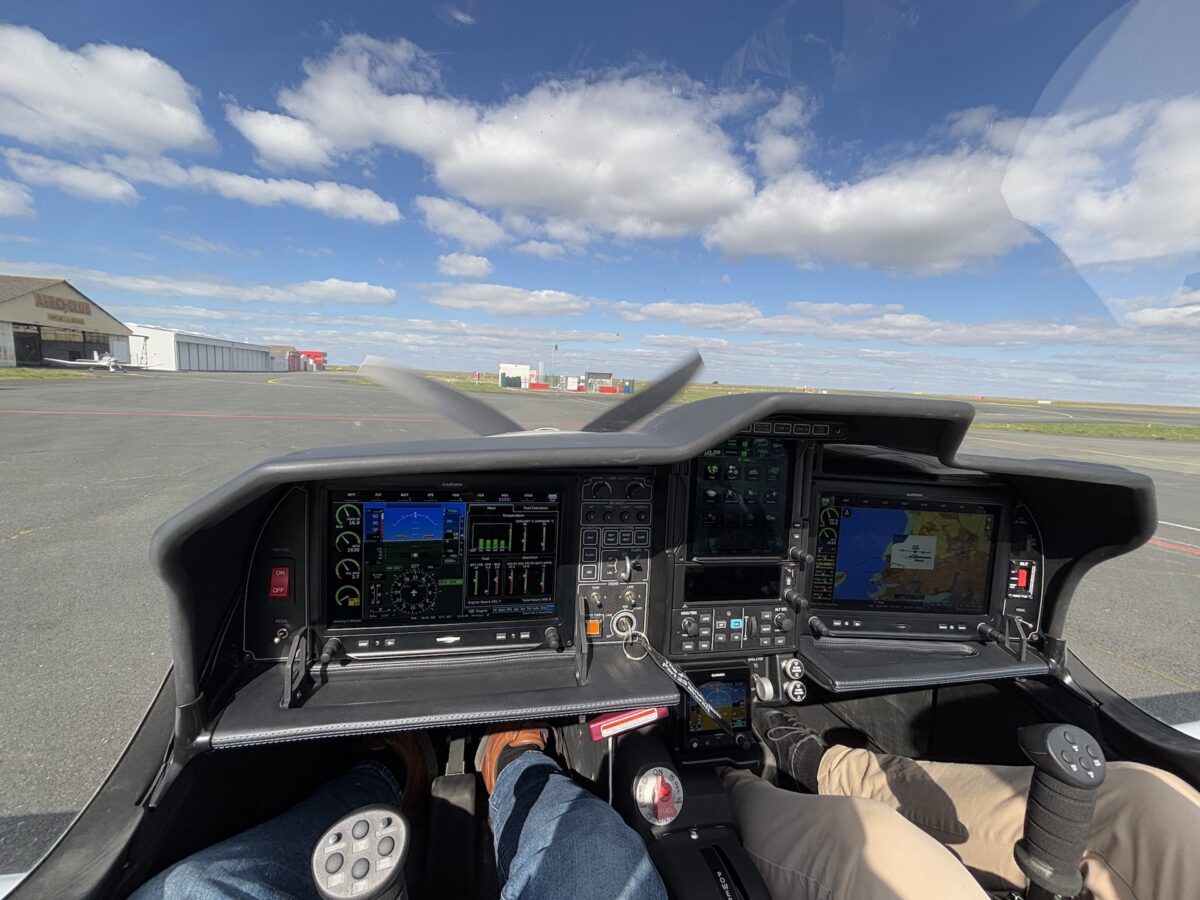
And the lighter weight of the airframe has given Elixir’s engineers room to maneuver to add reinforced landing gear without the added weight affecting the aircraft performance too much.
In case everything else fails Elixir’s aircraft comes equipped with a ballistic parachute, a feature that currently only Cirrus Aircraft, among the other players in the market, has made a default option. And the aircraft also has a black box, which, again, is something that is not standard in aircraft of this size.
But perhaps the best safety-enhancing feature is not designed with just safety in mind. One thing the Elixir Team learned from the sailing boat industry is that points of failure are often found at the interfaces, the joints that bond together two parts of an aircraft. This is where loads can often lead to things breaking and, in this regard, the OneShot simplified airframe proves its benefits once again.
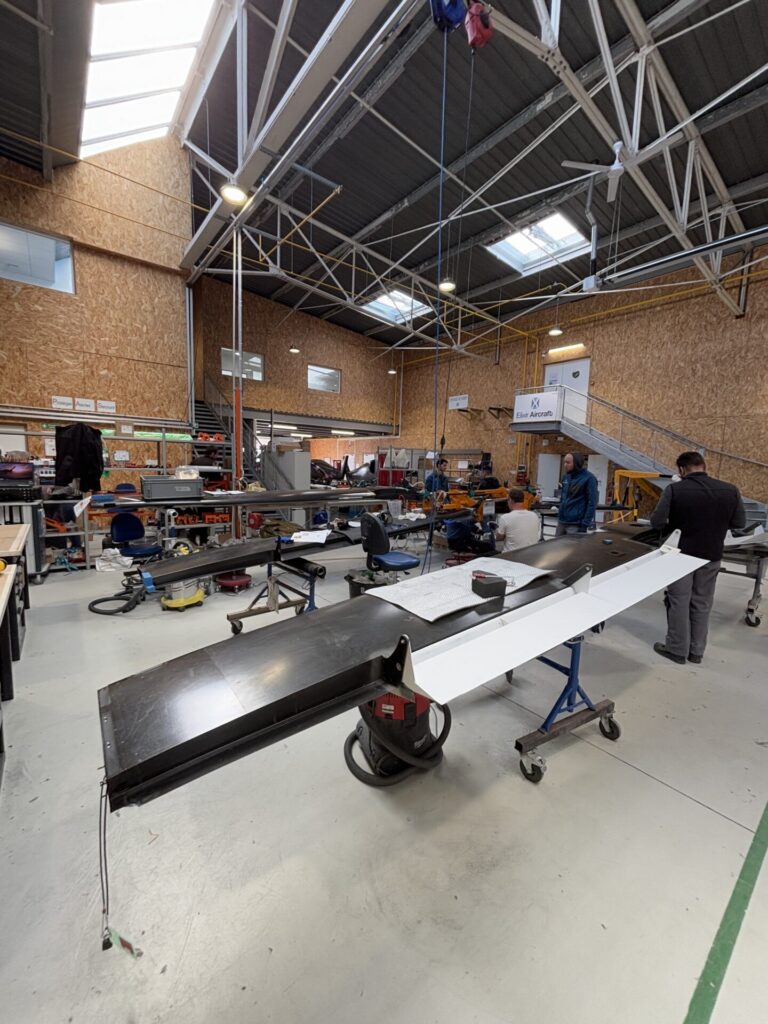
These advantages have been noticed in the industry.
“All major OEMs are moving in the same direction, towards composites,” Champenois, said. “And we think it is good that it becomes the industry norm.”
What’s next for Elixir Aircraft?
In February 2024, Elixir Aircraft announced it had raised an additional €13 million from a number of French institutional investors which included Innovacom, Bpifrance and the Nouvelle-Aquitaine Region, where La Rochelle is located. The funding round brought the total raised by Elixir Aircraft from external investors and through public innovation support programs to €40 million.
Elixir Aircraft has ambitious plans to deploy these funds to scale-up production, build the supply chain and step up hiring. The startup is already preparing to develop a plot of land next to its current facility in order to install a new, much larger, 160,000 sq ft final assembly line (FAL) which will allow it to dramatically increase production to up to 400 aircraft per year.
In addition to the 28 aircraft already delivered, as of February 2025 Elixir’s order book stood at 50 firm orders, effectively locking two full years of production at the current facility, and letters of intent for another 250 aircraft.
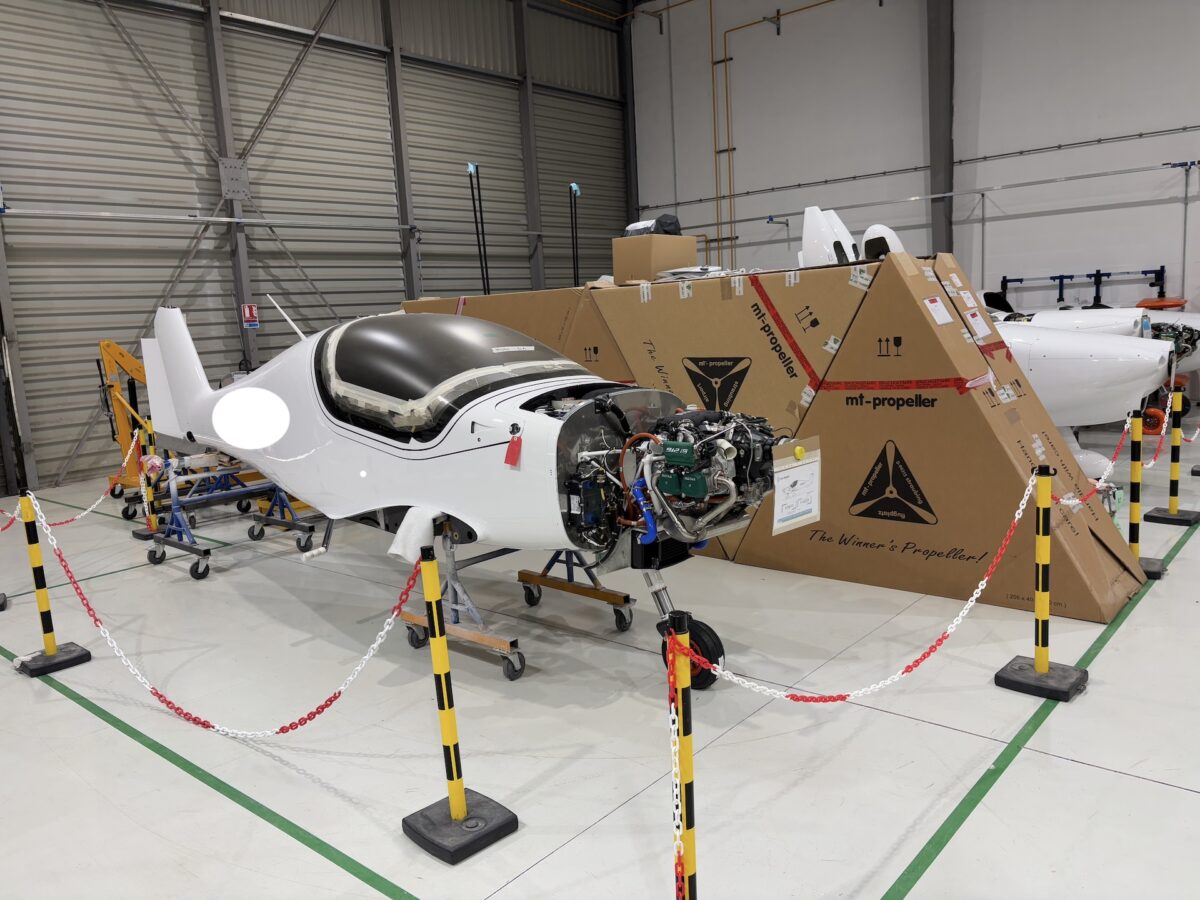
Days before our visit to La Rochelle, Elixir had announced a rather large order for 35 aircraft, placed by a US flight school.
Despite rumblings of an impending trade war between Europe and the United States, the latter remains the largest market for light aircraft in the world and one that Elixir Aircraft certainly has its eye on.
The French firm has already established a bridgehead in North America, with the 2024 announcement of the establishment of a re-assembly and customer service center which will employ200 staff at Sarasota Bradenton Airport (SRQ) in Florida. Champenois confirmed that if things go according to plan, Elixir’s Florida plant could become an additional FAL for the company.
Champenois was bullish about the prospects for this segment of the industry, referring to the fact that current industry production barely covers the replacement market, let alone the approximate 130,000 light aircraft that will eventually need to be replaced in the coming decades. While Cirrus, the most prolific of the lot, makes about 600 aircraft per year, most manufacturers are in the 200 aircraft per year range.
Champenois also referred to the need to bring innovation to the flight training space since this will also help sustain the pipeline of career vocations in aviation and ensure the future of the industry in the longer term.
“The first generation of light aircraft was in the 1920s, the second came in the 1950s, this is the generation of the best–selling and ubiquitous Cessna 172, and the third was in the 1970s,” he said. “And now we are building the fourth generation. It’s the end of a 60-year cycle.”