An air compressor converts power into kinetic energy, compressing air for various applications. The motor drives this compressor, providing the necessary energy.
Air compressors are essential tools in various industries, from automotive to construction. They provide compressed air for powering tools, inflating tires, and operating machinery. Understanding the relationship between an air compressor and its motor is crucial for effective operation. A reliable motor ensures efficient performance and longevity of the compressor.
Choosing the right type of motor can enhance energy efficiency and reduce operational costs. Knowing how to maintain both components can prevent breakdowns and extend their lifespan. This guide will explore the key aspects of air compressors and motors, helping you make informed decisions for your projects.
Introduction To Air Compressor And Motor Maintenance
Keeping your air compressor and motor in top shape is crucial. Regular maintenance boosts efficiency and extends lifespan. Understanding how to care for these machines helps avoid costly repairs.
Importance Of Regular Maintenance
Regular maintenance is essential for both air compressors and motors. It ensures they function smoothly. Here are some key reasons to maintain your equipment:
- Prevents Breakdowns: Regular checks catch issues early.
- Improves Safety: Well-maintained machines reduce hazards.
- Enhances Efficiency: Efficient machines save energy.
- Extends Lifespan: Proper care increases the life of the equipment.
Impact On Performance And Longevity
Maintenance directly affects the performance of air compressors and motors. Here’s how:
Factor | Impact on Performance | Impact on Longevity |
---|---|---|
Lubrication | Reduces friction and heat | Prevents wear and tear |
Clean Filters | Improves air quality | Prevents damage from debris |
Regular Inspections | Identifies potential issues | Extends operational life |
Neglecting maintenance leads to poor performance and reduced lifespan. Take action now to protect your investment.

Credit: dynamic-tools.en.made-in-china.com
Identifying Common Issues
Air compressors and motors are vital tools in many industries. Regular maintenance is key to longevity. Knowing the common issues can save time and money. Here are some signs and troubleshooting tips to help you.
Signs Of Wear And Tear
Identifying wear and tear early can prevent major failures. Look for these common signs:
- Unusual noises during operation
- Increased vibration levels
- Frequent pressure drops
- Overheating of the motor
- Visible leaks of air or oil
Each sign indicates a potential issue. Act quickly to address them. Regular inspections can help catch these signs early.
Troubleshooting Basic Problems
Basic troubleshooting can resolve many issues. Follow these steps:
- Check the power supply: Ensure the compressor is plugged in.
- Inspect the air filters: Clean or replace if dirty.
- Examine the hoses: Look for cracks or leaks.
- Monitor the pressure gauge: Ensure it reads accurately.
- Test the safety valve: Ensure it opens when needed.
Use this table to summarize basic problems and solutions:
Problem | Possible Cause | Solution |
---|---|---|
No power | Disconnected power supply | Reconnect and check fuses |
Low pressure | Blocked filters | Clean or replace filters |
Overheating | Insufficient ventilation | Improve airflow around the unit |
These steps help troubleshoot effectively. Regular maintenance keeps your air compressor and motor running smoothly.
Routine Inspection Checklist
Regular inspections of your air compressor and motor are vital. They help ensure smooth operation and longevity. This checklist will guide you through daily, weekly, monthly, and yearly tasks.
Daily And Weekly Tasks
Daily and weekly inspections keep your equipment running efficiently. Follow these simple steps:
- Check Oil Level: Ensure the oil level is adequate.
- Inspect Hoses: Look for wear or damage.
- Check Filters: Clean or replace as needed.
- Examine Electrical Connections: Ensure they are secure.
- Listen for Unusual Noises: Identify any strange sounds.
For weekly tasks, perform the following:
- Inspect the pressure gauge for accuracy.
- Check for leaks in the system.
- Ensure the compressor is securely mounted.
Monthly And Yearly Inspections
Monthly and yearly inspections provide a deeper check-up. These tasks are crucial for long-term performance.
Frequency | Inspection Task |
---|---|
Monthly |
|
Yearly |
|
Maintain a log of all inspections. This practice helps track performance and identify patterns. A well-maintained air compressor and motor can save time and money.
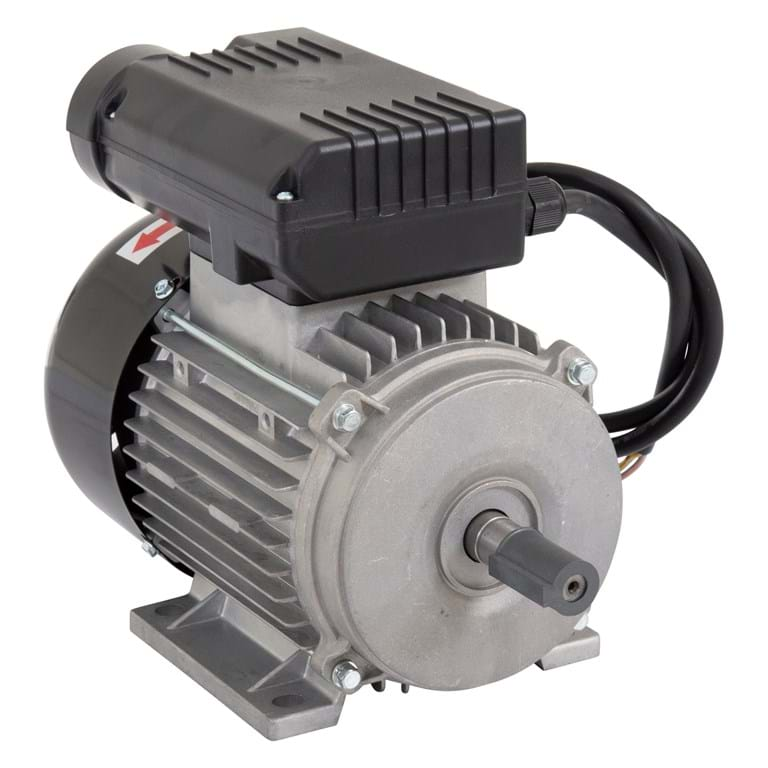
Credit: www.stanleyproducts.com.au
Cleaning And Lubrication Practices
Cleaning and lubrication are vital for your air compressor and motor. These practices enhance performance and prolong life. Regular maintenance prevents breakdowns and costly repairs.
Proper Cleaning Techniques
Cleaning your air compressor and motor involves a few essential steps:
- Turn Off Power: Always disconnect power before cleaning.
- Inspect Filters: Check and clean or replace air filters regularly.
- Wipe Down Surfaces: Use a damp cloth to clean exterior surfaces.
- Check for Dust: Remove dust from vents and internal parts.
- Clear Drain Valve: Ensure the drain valve is free of debris.
Use a vacuum for stubborn dust. Avoid using water directly on electrical parts.
Choosing The Right Lubricants
Proper lubrication is crucial for smooth operation. Follow these guidelines:
Type of Lubricant | Application | Frequency |
---|---|---|
Oil-based Lubricants | For general use in motors | Every 3 months |
Grease | For bearings and gears | Every 6 months |
Synthetic Oils | For high-performance motors | Every 12 months |
Always consult the manufacturer’s manual for specific lubricant recommendations. Use the right amount to avoid over-lubrication.
Belt Tension And Alignment
Proper belt tension and alignment are key for air compressor performance. Incorrect tension can lead to wear and tear. Misalignment can cause vibrations and damage. Regular checks keep your compressor running efficiently.
Adjusting Belt Tension
Correct belt tension ensures smooth operation. Follow these steps to adjust:
- Turn off the air compressor.
- Locate the tension adjustment mechanism.
- Use a tension gauge for accurate measurement.
- Adjust the tension until it meets the manufacturer’s specifications.
- Check for proper tension by pressing the belt. It should move slightly.
Too much tension causes stress on bearings. Too little tension leads to slippage.
Ensuring Correct Alignment
Alignment is critical for optimal performance. Misaligned belts can cause:
- Increased wear on components
- Excessive vibrations
- Reduced efficiency
To ensure correct alignment:
- Check the pulleys for alignment using a straightedge.
- Adjust the position of the motor if necessary.
- Make sure the belt sits evenly on the pulleys.
Use a laser alignment tool for precise adjustments. Regular checks extend the life of your air compressor.
Air Filters And Air Dryers
Air filters and air dryers play a crucial role in maintaining air compressors. They ensure clean, dry air flows through the system. This helps improve performance and extends the life of the equipment.
Regular Filter Replacement
Filters trap dust, dirt, and other contaminants. Regular replacement keeps the air clean and efficient. Here are key points to remember:
- Check filters every month.
- Replace filters every three to six months.
- Use manufacturer-recommended filters.
A dirty filter can cause:
- Reduced airflow.
- Higher energy costs.
- Poor compressor performance.
Keep track of your filter replacement schedule. This simple step can save money and time.
Maintaining Air Dryers
Air dryers remove moisture from compressed air. Proper maintenance ensures they work effectively. Follow these tips for optimal performance:
- Inspect the air dryer regularly.
- Clean the condensate drain.
- Check for leaks and fix them immediately.
Consider these maintenance tasks:
Task | Frequency | Description |
---|---|---|
Inspect filters | Monthly | Ensure filters are clean and functional. |
Replace desiccant | Every 6 months | Maintain moisture-absorbing capability. |
Check connections | Quarterly | Ensure all connections are tight and secure. |
Regular maintenance of air dryers prevents breakdowns. This keeps operations smooth and efficient.
Electrical Connections And Motor Health
Maintaining proper electrical connections is crucial for motor health. Faulty connections can lead to reduced performance. They may also cause damage to the air compressor motor.
Inspecting Electrical Components
Regular inspection of electrical components ensures optimal motor performance. Here are key components to check:
- Wiring: Look for frayed or damaged wires.
- Connectors: Ensure all connections are tight and secure.
- Fuses: Check for blown fuses and replace them.
- Switches: Test switches for proper operation.
Use a multimeter to measure voltage and resistance. This helps identify any issues quickly.
Monitoring Motor Performance
Regular monitoring of motor performance can prevent major issues. Here are important aspects to consider:
Aspect | What to Monitor |
---|---|
Temperature | Check for overheating signs. |
Vibration | Look for unusual vibrations. |
Noise | Identify any abnormal sounds. |
Keep a log of these observations. This helps track performance over time. Early detection of issues leads to timely repairs.
Regular maintenance of electrical connections promotes longer motor life. Stay proactive to ensure your air compressor runs smoothly.
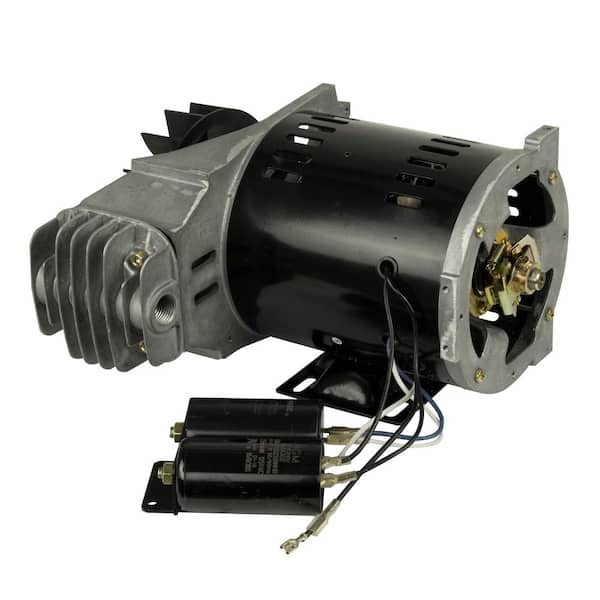
Credit: www.homedepot.com
Professional Maintenance And Repairs
Regular maintenance and timely repairs are key for your air compressor and motor. Proper care ensures optimal performance and extends their lifespan. Professional services help identify issues before they become major problems.
When To Call A Professional
Recognizing the signs that indicate a need for professional help is essential. Here are some common indicators:
- Unusual Noises: Loud or strange sounds during operation.
- Inconsistent Pressure: Fluctuating air pressure levels.
- Overheating: Excessive heat can damage the unit.
- Frequent Breakdowns: Regular issues indicate deeper problems.
- Visible Damage: Cracks or leaks in the compressor body.
Addressing these signs quickly can prevent larger issues.
Understanding Repair Costs
Repair costs for air compressors and motors can vary widely. Factors include:
Factor | Estimated Cost |
---|---|
Minor Repairs | $50 – $150 |
Major Repairs | $150 – $500 |
Replacement Parts | $20 – $300 |
Labor Costs | $75 – $150 per hour |
Understanding these costs helps budget for necessary repairs. Always request a detailed estimate before proceeding.
Investing in professional maintenance protects your equipment. Regular check-ups can save money in the long run.
Keeping Maintenance Records
Maintaining an air compressor and motor requires careful attention. Keeping accurate maintenance records is essential. It helps track service history and alerts you to potential issues. A well-maintained log can prevent costly repairs and downtime.
Logging Service Dates
Logging service dates is the first step in maintaining your equipment. Create a simple chart or table to record essential details. Include the date, type of service, and technician’s name. Here’s a sample table:
Date | Service Type | Technician |
---|---|---|
2023-01-15 | Oil Change | John Doe |
2023-03-22 | Filter Replacement | Jane Smith |
Update this log regularly. This practice helps you remember when the last service occurred. Set reminders for upcoming maintenance tasks.
Benefits Of A Maintenance History
A maintenance history offers many advantages. Here are some key benefits:
- Predictive Maintenance: Anticipate potential issues before they arise.
- Cost Savings: Regular maintenance reduces repair costs.
- Operational Efficiency: Well-maintained equipment operates smoothly.
- Safety: Regular checks ensure safe operation.
- Resale Value: A complete maintenance record boosts resale value.
Invest time in maintaining accurate records. This simple act pays off significantly. Your air compressor and motor will thank you.
Conclusion: Ensuring Operational Efficiency
Maintaining your air compressor and motor boosts performance. Efficiency saves energy and reduces costs. Regular care prevents breakdowns and extends lifespan.
Recap Of Key Points
- Understand your air compressor: Know its parts and functions.
- Regular maintenance: Check for wear and tear.
- Clean filters: Dirty filters reduce efficiency.
- Monitor pressure levels: Keep within recommended ranges.
- Inspect wiring: Ensure no frays or loose connections.
Final Thoughts On Preventative Care
Regular checks can prevent major issues. Schedule routine inspections. Follow these tips for better efficiency:
- Change oil regularly.
- Lubricate moving parts.
- Keep the area clean.
- Train staff on proper use.
Investing time in preventative care pays off. Efficient systems mean lower costs and less downtime. Keep your air compressor and motor running smoothly.
Frequently Asked Questions
What Is An Air Compressor And Motor?
An air compressor is a device that converts power into kinetic energy, compressing air for various applications. The motor powers the compressor, driving the pistons or rotary screws. Together, they create pressurized air used in tools, painting, and inflating tires, enhancing efficiency in various tasks.
How Do Air Compressors Work?
Air compressors work by drawing in ambient air, compressing it, and storing it in a tank. The motor drives the compressor mechanism, which reduces the air volume, increasing pressure. This stored compressed air can be used immediately or later, powering tools and equipment as needed.
What Are The Types Of Air Compressors?
There are several types of air compressors, including reciprocating, rotary screw, and centrifugal compressors. Reciprocating compressors use pistons, while rotary screw compressors utilize two rotating screws. Centrifugal compressors, on the other hand, use a rotating disk to increase air velocity.
Each type suits different applications and requirements.
How To Maintain An Air Compressor?
To maintain an air compressor, regularly check and change the oil, clean the air filter, and drain the moisture from the tank. Inspect hoses and connections for leaks and ensure the motor operates smoothly. Regular maintenance prolongs the compressor’s life and enhances performance.
Conclusion
Choosing the right air compressor and motor is essential for efficiency and performance. Understanding their functions helps you make informed decisions. Regular maintenance can extend the lifespan of your equipment. Invest wisely to ensure optimal operation. This knowledge will enhance your projects and boost productivity in the long run.