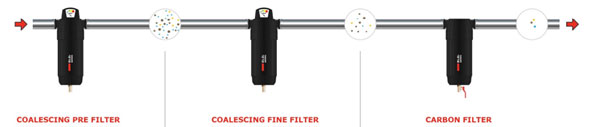
Coalescing Pre filter: Remove solid particles like dirt, rust, and dust
Filtration Grade: Removes the wet particle down to 1 micron and oil aerosols down to 0.1 mg/m3
Air Quality: ISO 8573-1:2010 (2:-:2)
Maintenance Schedule: Element to be replaced every 12 months or when DP gauge is in red
Coalescing Fine Filter: Remove oil aerosols and finer particulates
Filtration Grade: Removes the wet particle down to 0.01 micron and oil aerosols down to 0.01 mg/m3
Air Quality: ISO 8573-1:2010 (1:-:1)
Maintenance Schedule: Element to be replaced every 12 months or when DP gauge is in red
Activated Carbon Filters: Remove oil vapours and odours for applications requiring odour-free air
Removes the oil vapour down to 0.003 mg/m3
Air Quality: ISO 8573-1:2010 (1:-:1)
Maintenance Schedule: Element to be replaced every 6 months
Air Dryers
Air dryers remove moisture from the compressed air, preventing corrosion and other problems
What is dew point? Dew point is the temperature at which the water vapour within the air condenses into dew or frost
Pressure dew point (PDP) is the temperature at which the water vapour in the compressed air condenses into water
Major Types of Air Dryers
Refrigerated Dryers: These use a refrigeration cycle to cool the air and condense and remove the moisture; suitable for general applications to achieve PDP of 3 Dec C.
Cycling Dryers – Saves energy in Compressors with VFD and Multi compressor setup
Non-Cycling Dryers – Fixed power consumption at all conditions
Maintenance Schedule: Refrigerated dryers are generally maintenance free and do not need frequent maintenance activities except for the maintenance checks/activities given below
Replace PF and FF elements if the filters are in built in the dryers once in a year
Check and replace auto drain valve/kits once in a year
Desiccant Dryers: Use desiccant materials to adsorb moisture; ideal for applications requiring extremely dry air.
Heatless Regenerative Dryers: Remove moisture from compressed air without the use of external heat using the desiccant materials like silica gel or activated alumina to adsorb moisture from the compressed air. A portion of the compressed air is used to regenerate the saturated desiccant.
Advantages:
No external heat required: Saves energy and reduces operating costs.
Simple design: Easy to install and maintain.
Compact size: Suitable for applications with limited space.
Limitations:
High purge air consumption: Can result in significant air loss.
Limited to lower flow rates: Not ideal for very high compressed air demands.
Heatless dryers typically achieve PDPs in the range of -40°C. Some specialized models can reach even lower PDPs, down to -70°C.
Heated Blower Purge Dryers: Also known as heat-regenerated dryers, are a type of desiccant air dryer that uses a combination of a blower and a heater to regenerate the desiccant material. This makes them more energy-efficient than heatless dryers, especially for larger flow rates
Advantages:
Energy Efficiency: Lower operating costs compared to heatless dryers, especially for larger flow rates.
Lower Purge Air Consumption: Reduces air loss and improves overall system efficiency.
Stable Dew Point: Provides a consistent and stable dew point, suitable for demanding applications.
Limitations:
Higher Initial Cost: More expensive to purchase compared to heatless dryers.
More Complex: Requires more complex control systems and maintenance.
Standard PDP: Most heated blower purge dryers can reliably achieve a PDP of -40°C. This is a common standard for many industrial applications requiring dry compressed air.
Heat of Compression Dryers are a unique type of desiccant air dryer that leverages the heat generated during the compression process itself to regenerate the desiccant material.
This makes them incredibly energy-efficient, as they don’t require separate heaters or blowers for regeneration.
Advantages
Unique advantage: One of the key advantages of heat of compression dryers is that they achieve these low PDPs without requiring any external heating or blowers. This is because they utilize the heat generated during the compression process itself, making them highly energy efficient.
High Energy Efficiency: No external heat or blowers are required for regeneration, resulting in significant energy savings.
Low Operating Costs: Reduced energy consumption translates to lower running costs.
Environmentally Friendly: By utilizing waste heat, these dryers contribute to energy conservation.
Limitations:
Requires Oil-Free Compressor: To prevent contamination of the desiccant, these dryers must be used with oil-free air compressors.
High Initial Cost: The initial investment for heat of compression dryers can be higher compared to other types.
Heat of compression dryers can typically achieve PDPs in the range of -20°C to -40°C.
Membrane Dryers: Use permeable membranes to separate water vapor; suitable for smaller systems. utilize a fascinating process called selective permeation to remove moisture from compressed air.
At the heart of a membrane dryer lies a bundle of tiny, hollow fibers made of a special polymer material. These fibers have a unique property: their walls are selectively permeable, meaning they allow certain molecules to pass through while blocking others. In this case, water vapor is allowed to permeate, while dry air (mainly nitrogen and oxygen) is not
Advantages:
Simple and Compact: They have a simple design with no moving parts, making them compact and easy to install.
Low Maintenance: Due to the absence of moving parts, they require minimal maintenance.
Quiet Operation: They operate silently, making them suitable for noise-sensitive environments.
No Power Required: They don’t need electricity to operate, saving energy.
Limitations:
Limited Flow Rate: They are best suited for lower flow rate applications.
Not for Very Low Dew Points: They may not achieve the extremely low dew points attainable with desiccant dryers.
Purge Air Loss: The continuous purge air flow results in some loss of compressed air.
Membrane dryers usually achieve PDPs in the range of +10°C to -40°C (50°F to -40°F
Moisture Separators: Remove bulk water and larger droplets from the air before it enters filters or dryers. Moisture separators are essential devices used to remove water droplets from air or gas streams. This is crucial in many industrial processes to protect equipment, improve efficiency, and ensure product quality. Here’s how they generally function:
Separation
Inertial Separation: This method relies on the principle of inertia. The moist air or gas stream is forced to change direction abruptly. Due to their higher inertia, the heavier water droplets continue moving in a straight line and collide with a surface, where they accumulate.
Centrifugal Separation: This technique uses centrifugal force to separate moisture. The air or gas stream is spun rapidly, causing the denser water droplets to be flung outwards and collected on the walls of the separator.
Coalescing Separation: This method uses a filter or a porous medium to cause small water droplets to combine into larger ones. These larger droplets are then easier to separate by gravity.
Collection and Drainage
Once the water droplets are separated, they are collected in a sump or a collection chamber at the bottom of the separator. From there, the collected water is drained away, either manually or automatically using a drain valve or a trap.
Oil-Water Separators: Separate and collect oil from condensate for safe disposal, ensuring compliance with environmental regulations. Oil-water separators are crucial devices used to separate oil from water, preventing pollution and ensuring environmental compliance. Here’s a breakdown of how they function:
Separation
Gravity Separation: This is the most basic method, relying on the difference in density between oil and water. Oil is less dense than water, so it naturally rises to the surface. The separator provides a calm environment to allow this separation to occur.
Coalescence: This process involves encouraging small oil droplets to combine into larger ones. This makes them rise to the surface more quickly and easily. Coalescing media, like specially designed plates or filters, are used to facilitate this process.
Filtration: Some separators use filters to remove any remaining oil droplets that haven’t been separated by gravity or coalescence. These filters can be made of various materials that attract oil while repelling water.
Collection and Discharge
Once the oil is separated, it’s collected in a separate chamber or at the top of the separator.
The collected oil can then be removed for disposal or recycling. The cleaned water is discharged from the bottom of the separator, often undergoing further treatment before release
Air Receivers: Also known as air tanks, act as storage tanks and help reduce system pressure fluctuations, promoting smoother operation. They act as a storage reservoir for compressed air, providing several crucial functions:
Storage and Buffering: Air receivers store compressed air, acting as a buffer between the compressor and the point of use. This stored air helps to meet peak demands that may exceed the compressor’s immediate output. It also helps to smooth out pressure fluctuations caused by intermittent air usage.
Pressure Stabilization: By maintaining a volume of compressed air, receivers help to stabilize system pressure. This ensures a consistent air supply to tools and equipment, preventing performance issues due to pressure drops.
Moisture Separation: As hot, compressed air enters the receiver, it cools. This cooling causes moisture to condense, which can then be drained from the tank. This reduces the load on downstream dryers and filters, improving their efficiency and lifespan.
Energy Efficiency: Air receivers allow compressors to operate more efficiently. By reducing the frequency of compressor cycling, they minimize energy waste and wear and tear on the compressor.
Key Considerations for Air Receivers:
Size: The size of the receiver should be appropriate for the compressed air system’s demands. Larger receivers provide more storage capacity and better pressure stability.
Pressure Rating: The receiver must be rated to handle the maximum pressure of the compressed air system.
Material: Receivers are typically made of steel or aluminium, with corrosion-resistant coatings.
Safety Features: Safety features like pressure relief valves and drain valves are essential for safe operation.
Selecting the right air receiver is crucial for the efficiency and reliability of your compressed air system. Here’s a breakdown of the key factors to consider:
System Requirements
Air Demand: Determine the maximum airflow (CFM) required by your tools and equipment. Consider both continuous and peak demands.
Pressure Requirements: Identify the operating pressure (PSI) needed for your applications. Ensure the receiver’s pressure rating exceeds this.
Duty Cycle: Understand how frequently your tools and equipment will be used. A higher duty cycle may require a larger receiver.
Subscribe
Stay updated & get insights on the compressed air industry