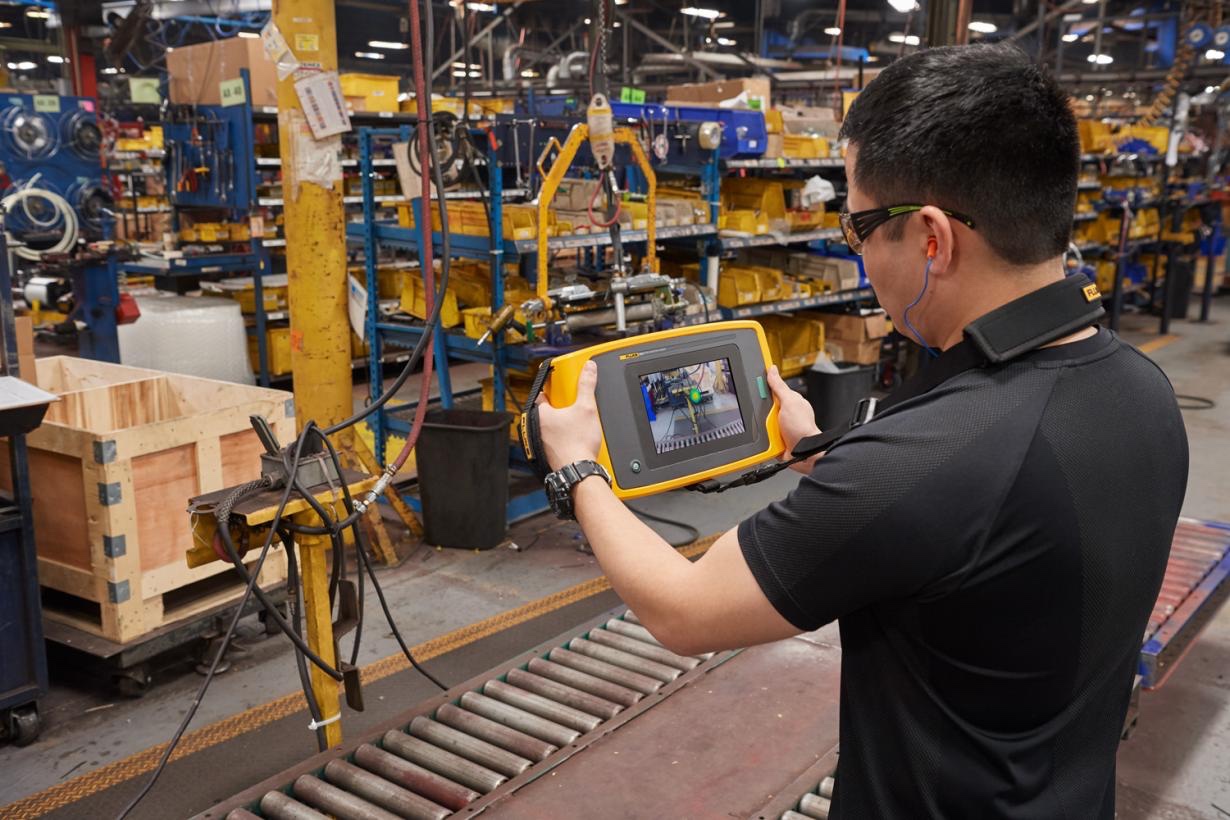
An industrial compressed air system is critical in many manufacturing and industrial operations. It provides the power needed to operate tools and equipment and must maintain trouble-free operations to ensure that production runs smoothly. However, the management and operation of compressors are only a small part of the maintenance tasks that industrial equipment operators must perform. Compressed air systems require substantial investments in capital and maintenance.
One of the critical areas of focus regarding compressed air systems is leakage. Leaks can lead to significant losses in compressed air, leading to increased energy costs and decreased efficiency. To effectively manage leaks and other issues in an industrial compressed air system, it’s important to understand the system dynamics and to conduct regular compressed air assessments.
Compressed Air Leak Assessment
A compressed air leak assessment is a multi-step process that helps identify leaks and other issues in the compressed air system. The assessment typically includes the following steps:
- Documentation: A thorough documentation of the compressed air system is performed, including the location of the compressors, air dryers, and other equipment.
- Eliminating leaks and demand: Leaks are identified and repaired, and efforts are made to reduce unnecessary demand on the compressed air system.
- Air assessments: A comprehensive compressed air system assessment is performed to identify any hidden issues that may be causing inefficiencies.
- Site survey: A site survey is conducted before the compressed air energy assessment to gather information about the facility and the compressed air system.
- Measure and quantify kW/100 cfm: The compressed air system’s kW/100 cfm is measured and quantified as part of the energy assessment.
- Implement recommendations: Based on the assessment findings, recommendations are made to improve the kW/100 cfm for the compressed air installation.
Benefits of Compressed Air Assessments
There are several benefits to performing regular compressed air assessments. By identifying leaks and other issues and implementing recommendations to improve efficiency, industrial equipment operators can see significant savings in energy costs. Additionally, by reducing demand on the compressed air system, equipment operators can prolong the life of their compressors and other equipment.
Another key benefit of compressed air assessments is that they help to verify the performance of kW/100 cfm for the compressed air systems. This can help industrial equipment operators identify areas to improve their energy efficiency and make more informed decisions about managing their compressed air systems.
In conclusion, managing leaks and other issues in an industrial compressed air system is crucial for maintaining efficient operations and reducing energy costs. By conducting regular compressed air assessments, industrial equipment operators can identify leaks, reduce demand, and improve the efficiency of their compressed air systems. This will help them save money and prolong the life of their equipment.
If you’re looking to improve the efficiency of your industrial compressed air system, contact Michigan Air Services for an air audit or any other compressor repair needs for your manufacturing facility. Our team of experts will work with you to ensure that your compressed air system runs at peak performance, saving you money and reducing downtime.