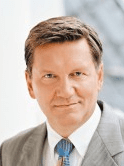
February 28, 2025, ©. Leeham News: We do a Corner series about the state of developments to replace or improve hydrocarbon propulsion concepts for Air Transport. We try to understand why the development has been slow.
Last week, we discussed the fact that Airbus has moved its hydrogen-fueled ZEROe aircraft into the 2040s and that it will be fuel cell based. It’s a bit of an irony that Pratt &Whitney announced major news for the alternative hydrogen burn alternative four weeks before. Let’s dissect that Pratt & Whitney announced.
Pratt & Whitney HySIITE
As I have written, the first jet engine, Hans von Ohain’s He S-1, Figure 1, started on hydrogen as it wouldn’t run on kerosene. Hydrogen is a good fuel for gas turbine-burn engines. It produces a cleaner burn than the kerosene-based Jet-A1, but it’s not as clean as the output of a fuel cell (which outputs pure water). A hydrogen burn gas turbine still produces NOx emissions, though several times lower than a Jet-A1 burn engine.
Pratt & Whitney has extensive experience with hydrogen-burn gas turbines. In 1958, the CIA wanted the Lockheed Skunkworks to build a successor to the U-2 spy plane that could fly up to Mach 2.5 at 100,000ft. Lockheed projected a CL-400 that looked like a twin-engined F-104, with the engines at the wingtips and liquid hydrogen in the fuselage. Pratt & Whitney built an LH2-burning engine for the program and ran it on a test stand, Figure 2. The project was canceled, but Pratt & Whitney had its first LH2 engine experience.
When hydrogen was revived as a possible fuel for airliner gas turbines, Pratt & Whitney received a contract from the US Department of Energy’s ARPA-E to study further development of the hydrogen burn process. The project, called HySIITE (Hydrogen Steam-Injected, Intercooled Turbine Engine), ended late last year after a two-year study of critical components and processes.
The critical process was burning hydrogen with compressor air pre-mixed with steam from water. A HySIITE engine uses a backflow core to put the needed extra components in the bypass stream in the right order, Figure 3. Bypass air for the core is captured at the rear of the engine and then routed forward through the core (blue arrows in Figure 3 that turn red after the combustor).
The components needed to generate the steam from the water, which is a result of the hydrogen oxidation in the combustor, are a large heat exchanger in the bypass stream (orange arrows in Figure 3) that cools the core exhaust (while transferring energy to the bypass stream).
The water in the cooled exhaust is then caught in centrifugal water separators further back, close to the nacelle skin (the blue circular arrows). The water is routed back to the core exhaust’s heat exchanger, where the first part is designed as a steam evaporator. The water is there heated to steam before entering the compressor upstream of the combustor (the white dotted path).
The results achieved by Pratt & Whitney were spectacular. In full-scale rig test of the critical processes and components conducted at the RTX Technology Research Center (East Hartford, CT), the following was seen:
- A single nozzle combustor rig test with H2 fuel demonstrated a 99.3% reduction in NOx compared to a current benchmark.
- A condenser demonstrated the capture of 1 gallon of water every 3 seconds (1.26 liters per second), meeting design requirements.
- An evaporator functioned effectively in an exhaust gas path, generating steam.
The results are that the HySIITE architecture could enable up to 35% improved energy efficiency compared to a current state-of-the-art Turbofan for a single-aisle aircraft.
The virtual elimination of NOx emissions removes the major negative aspect of the hydrogen burn alternative. The 35% energy efficiency makes hydrogen burn the only viable alternative for emission-free aircraft with over 100 seats (the size limit of fuel cell aircraft for the foreseeable future).
A change in the balance between Power to Liquid Hydrogen or SAF-fueled aircraft
The change in energy efficiency derived in the HySIITE turns the power equation for LH2 versus SAF in a Power to Liquid process. This end-to-end discussion on what shall be the future emission-neutral fuel for larger airliners is the subject of the next Corner.
Related