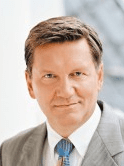
March 7, 2025, ©. Leeham News: We do a Corner series about the state of developments to replace or improve hydrocarbon propulsion concepts for Air Transport. We try to understand why the development has been slow.
Last week, we wrote about Pratt & Whitney’s announcement in January: their trials with critical components of their HySIITE engine, Figure 1, showed that they could increase the efficiency of a hydrogen burn engine by 35%!
It does this by intelligently using the water released when hydrogen oxidizes with the air’s oxygen. The water separated from the exhaust is reheated into steam and entered into the engine’s combustion, reducing NOx by 99.3% and increasing the engine efficiency by 35%.
HySIITE changes the PtL SAF and Green Hydrogen balance
The 35% increase in efficiency of a HySIITE engine gives hydrogen-burn-engined airliners a clear efficiency advantage when comparing the complete energy consumption from “Well to Use” between SAF produced from renewable energy, so-called PtL SAF, and hydrogen produced from the same energy.
SAF can be produced through different methods, described in this Corner. Of these, the Power-to-Liquid SAF has no limitations on raw material supply.
To understand how hydrogen and PtL SAF are produced, see Figure 2 and the text below. It’s from an Airbus website describing the process.
PtL is a synthetically produced liquid hydrocarbon. Renewable electricity is the key energy source, and water and carbon dioxide (CO₂) are the main resources used in SAF PtL production, which consists of three main steps:
- Renewable energy powers electrolyzers to produce green hydrogen.
- Climate-neutral CO₂ – captured via, for example, Direct Air CarbonCapture – is converted into carbon feedstock.
- Carbon feedstocks are synthesized with green hydrogen—via processes such as Fischer-Tropsch—to generate liquid hydrocarbons. These are then converted to produce a synthetic equivalent to kerosene.
The process in Step 1 produces Green Hydrogen, avoiding the cost of CO2 capture in Step 2 and combining hydrogen with Carbon to produce PtL in Step 3. That’s why hydrogen organically is a lower-cost fuel than PtL at the production level.
A major advantage of PtL is that it can be transported and distributed via the existing network of fossil-fuel infrastructure, including pipelines and filling stations. It can also be filled in existing aircraft tanks and burned in existing engines.
To compensate for these advantages, hydrogen must be considerably cheaper to use than PtL SAF. This is where HySIITE changes the balance.
Figure 3 shows the energy use in a Pathway analysis presented by RTX Chief Scientist Dr. Michael Winter and Pratt &Whiney’s Technical Fellow Neil Terviliger at the January briefing.

Figure 3. PtL SAF and LH2 pathway data were presented during the January briefing. Source: RTX and Pratt & Whitney.
The hydrogen burn alternative before HySIITE held an 8% energy use advantage versus a PtL SAF alternative. This advantage is so low that one must ask if the investments needed in infrastructure to supply LH2 to the planes and the changes to the aircraft are motivated.
The water recovery and reuse in HySIITE increase the advantage threefold, making a future hydrogen supply system and aircraft more attractive.
In summary, the HySIITE process produces engines with the following advantages:
- LH2 engines with the HySIITE process are 35% more efficient than today’s equivalent technology engines.
- The NOx emissions are essentially eliminated.
- The contrail formation problem of an LH2 engine is addressed.
- The net energy savings versus PtL are tripled.
Water makes Gas Turbine Engines more efficient
We have seen how capturing and re-injecting the water as steam into the HySIITE process makes the engine more efficient. The reason is that as fuel is burned in the combustor to produce a high-speed gas that drives the turbines and the fan, the mass of the gas is essential. Air at typical cruise heights has 1/4 of ground-level density. As it is compressed in the compressor, the density increases, but an air+steam mix at the same compression level will have a much higher density.
The increase in density (i.e., mass per volume) increases the power extraction in the turbines, which increases the engine’s efficiency.
Water is also produced in kerosene-burn engines but at a smaller scale. MTU, behind the WET engine process, thinks it’s still worth doing. We will discuss this engine and its process in the next Corner.
Related