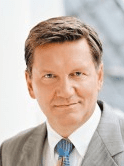
January 31, 2025, ©. Leeham News: We do a Corner series about the state of developments to replace or improve hydrocarbon propulsion concepts for Air Transport. We try to understand why the development has been slow.
We have covered the progress of battery-based aircraft and hybrids, both serial and parallel hybrids. A couple of mild hybrids have a larger chance of success than the ones we described. We will look into these and then start looking at different hydrogen-fueled alternatives.
The Aeronautical Mild Hybrid
In last week’s Corner, we described that full-size hybrids have not proliferated outside trial systems on test aircraft. To my knowledge, not a single hybrid aircraft is in certification or preparing for serial production, outside of the mild hybrid Volt Aero Cassio described below.
We discussed this last week: Full hybrid propulsion systems are complex, heavy, and expensive. Their real-world operational improvement in terms of hydrocarbon fuel burn is modest. When all factors are considered, the Direct Operating Cost, DOC, of a hybrid aircraft, which includes the capital cost of a more complex aircraft, is not attractive. This is the main reason no full-hybrid aircraft are nearing certification or production.
There are two exceptions to this observation; both are mild hybrid concepts.
Aircraft Mild Hybrids
Volt Aero’s Technical Director & Test Pilot, Didier Esteyne, knows his stuff. He’s the person behind the Airbus E-Fan prototypes that flew for the first time at the 2014 Farnborough Air Show. Didier developed a mild hybrid propulsion system for Volt Aero’s Cassio aircraft (Figure 2), where the battery is kept reasonable in size and mass by only using electric flight around the airport. As batteries improve, the climb and cruise thermal engine part of flights can be made shorter, reducing the thermal engine fuel burn and pollution.
Engine mild hybrids
Engine OEMs have auxiliary gearboxes connected to their core shafts to zap power to drive hydraulic pumps and electric generators, Figure 1. The gearbox and shaft also put power into the shaft for engine start. It’s done today via a bleed system air starter. It’s not far-fetched to change the generator to a generator/motor and use the motor for engine start and also to help the engine with transient management.
With such a concept, the engine can be designed with tighter margins to compressor stall, thus increasing engine efficiency. The efficiency gain is around 5%, but the low complexity investment required makes it worthwhile. Once again, the most critical component is the energy store battery required. That’s why the system is not involved in propulsion assistance but in engine management, as otherwise, a heavy battery would negate the gains.
So, virtually all engine manufacturers and airframers will announce hybrids, but these will be very mild hybrids of the type described. If the word hybrid weren’t so charged from the automobile industry, no one would use the word hybrid for a system that helps gas turbines manage transients of perhaps half a minute.
Hydrogen propulsion concepts
With hybrid propulsion covered, we will now look at the latest trends in hydrogen-fueled propulsion systems.
There have been interesting recent developments, especially for the gas turbine hydrogen-burn alternative. Pratt & Whitney has developed new technology to virtually eliminate the NOx emissions plaguing this alternative while increasing end-to-end efficiency.
The alternative to hydrogen-burn gas turbine solutions is fuel cell-based systems, where the fuel cell produces electricity from hydrogen reacting with the air’s oxygen, with water as a result. The electricity produced is powering electric motors, as in the battery and hybrid alternatives. Progress has been made on lighter, more efficient fuel cell technologies.
We will spend several Corners on the hydrogen developments, starting with hydrogen burn next week and going into detail on the new technologies and ideas developing there.
Related