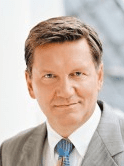
February 7, 2025, ©. Leeham News: We do a Corner series about the state of developments to replace or improve hydrocarbon propulsion concepts for Air Transport. We try to understand why the development has been slow.
We have covered the progress of battery-based aircraft and hybrids, where the last Corner was about the most sensible hybrids, the mild hybrids. Now, we turn to hydrogen-fueled alternatives.
The Fuel Cell propulsion system
In previous Corners, we described the principle and key attributes of an aeronautical fuel cell-based propulsion system. Here, we focus on developments over the last years.
The hydrogen fuel cell (Figure 1) lets the hydrogen react with the air’s oxygen, thus producing water. In the process, electrons are freed and travel outside the fuel cell as current to run the “balance of plant” components (Figure 2, showing compressor to keep air pressure up at altitude, humidifier to keep the fuel cell PEM membrane moist, cooling radiators, etc.) and deliver electric power to electric propulsion motors that drive propellers or fans.
The challenges with hydrogen fuel cells are:
- The storage of hydrogen aboard the aircraft. Hydrogen weighs 36% of Jet fuel for the same energy content, but it takes four times the space if stored as a liquid at -253°C. The need for a Dewar flask-type tank with low heat losses makes the storage of hydrogen difficult (it needs to be a semi-cylindrical double-wall tank with a vacuum between the walls). The problematic hydrogen storage is shared with the burn alternative, but some new ideas there reduce the problem to the hydrogen consumed during a mission. For a fuel cell system, we need both mission and reserve hydrogen in the Dewar tank.
- The fuel cell process generates a lot of heat. Of all the components needed in a fuel cell system, the heat management parts (called radiators in Figure 2) are the heaviest. These create the most drag due to the funneling of cooling air through the radiators’ heat exchangers. The problem is aggravated for low-temperature fuel cells by the process happening at 80°C, which gives a low-temperature delta to the surrounding cooling air. It forces large heat exchanger areas, which creates airframe drag.
- The fuel cell and its balance of plant components are heavy, considerably heavier than the gas turbine turboprops or turbofans these replace.
- Fuel cell aircraft rely on liquid hydrogen (LH2) being available at airports. This is a major problem where any solution will take time.
Positive developments for fuel cells are:
- A high-temperature fuel cell operates at double the normal fuel cell temperature, 160°C. It makes for a more efficient heat exchange with the surrounding air. ZeroAvia is working on a high-temperature fuel cell that is air-cooled. It has the potential for gains in mass versus classical systems. However, the volume of this system creates a space problem. The progress in making these high-temperature modules available to the market has been slow.
- A fuel cell system with a well-designed compressor/turbine part (right side in Figure 2) can maintain efficiency at altitude. A practical limit is presently 25,000ft, the typical altitude limit of a Turboprop like ATR72. Given adequate cooling, the fuel cell and electric motor will not experience the power lapse that a gas turbine has with increasing altitude.
Limits in size for fuel cell airliners
The airframe projects using fuel cell propulsion systems have given a 100-seat turboprop aircraft operating up to Flight Level 250 as a practical limit for fuel cell systems. Beyond this size, heat management, and thus mass and volume, is difficult. The power level needed for such an aircraft would be propulsion units with around three Megawatts per side of the plane.
Present systems in development are at 0.6 MW, with 2MW units planned for later introduction. We need to see a certified, operationally used implementation before one can judge the future of fuel cell systems in airliners. It has the problem of all hydrogen-based projects: how to get hydrogen to the airport and fuel the aircraft.
Related