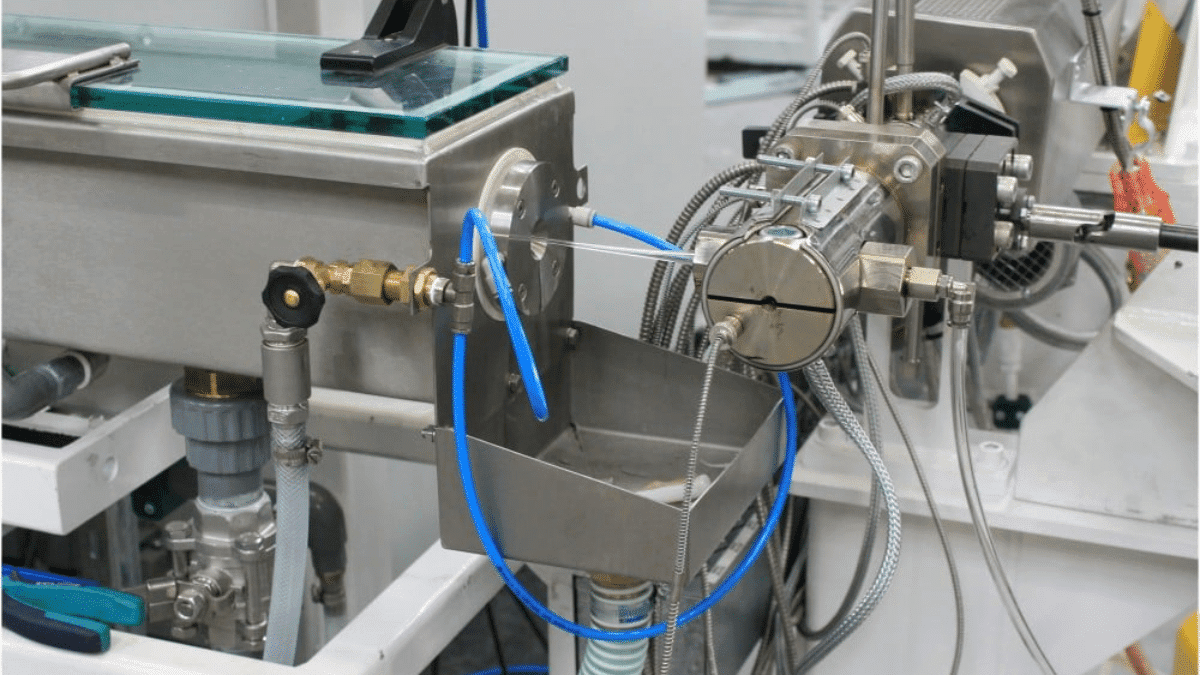
Every piece of medical equipment tells a story of innovation, and at the heart of many life-saving devices lies a critical manufacturing process few people ever consider: medical tubing extrusion. From IV lines to catheters, from surgical drainage tubes to complex diagnostic equipment components, extruded medical tubing represents an unsung hero of modern healthcare.
Extruders for Medical Tubing
Medical tubing extrusion equipment represents one of the most precise manufacturing processes in modern industry. Unlike standard industrial extrusion, medical tubing demands extraordinary levels of consistency, cleanliness, and performance. Specialized medical-grade extruders are engineered to meet these rigorous requirements, featuring advanced control systems that monitor every aspect of production.
The extrusion process begins with carefully selected raw materials fed into a precisely controlled machine. Single and twin-screw extruders dominate medical tubing production, with twin-screw systems offering superior mixing and material consistency. These machines operate in highly controlled environments, often within clean rooms that minimize potential contamination.
Manufacturers must navigate complex regulatory landscapes, with each tube potentially subject to extensive testing and certification. Medical-grade extrusion goes far beyond simply creating a tube, it’s about ensuring patient safety through absolute precision and quality control.
Materials of Medical Tubing
Medical tubing relies on a diverse range of specialized polymers, each selected for specific performance characteristics:
- Polyurethane (PU) offers exceptional flexibility and biocompatibility, making it ideal for long-term implantable devices. Its ability to withstand body chemistry while maintaining structural integrity sets it apart from other materials.
- Polyamide (PA) provides excellent mechanical strength and heat resistance. Commonly used in applications requiring durability and precision, PA tubing finds applications in complex medical devices and surgical instruments.
- Polyvinyl Chloride (PVC) remains a cost-effective option for many medical applications, particularly disposable medical equipment. Its versatility and ease of manufacturing make it a staple in healthcare tubing.
- Thermoplastic Elastomers (TPE) bring remarkable flexibility and softness to medical tubing. These materials excel in applications requiring gentle patient contact or specialized movement characteristics.
- Polypropylene (PP) offers chemical resistance and lightweight properties, making it valuable in laboratory and diagnostic equipment tubing.
- Polyethylene (PE) provides excellent chemical inertness and is often used in applications requiring minimal material interaction.
- Ethylene-Vinyl Acetate (EVA) combines flexibility with good chemical resistance, finding use in specialized medical applications that require unique material properties.
Precision and Calibration
The true marvel of medical tubing extrusion equipment lies in its extraordinary precision. Modern extrusion systems can produce tubes with tolerances measured in micrometers, while advanced optical measurement systems continuously monitor tube diameter, wall thickness, and surface consistency in real-time.
Calibration represents a critical step in the process. Sophisticated cooling systems and precise diameter control mechanisms ensure that each tube meets exact specifications. Some medical tubes require wall thickness variations as small as 0.01 millimeters – a level of precision that pushes the boundaries of manufacturing technology.
Quality control goes beyond physical measurements. Each batch of medical tubing undergoes rigorous testing for biocompatibility, chemical resistance, and structural integrity. That’s why manufacturers must maintain extensive documentation, tracking every aspect of production to meet stringent medical device regulations.